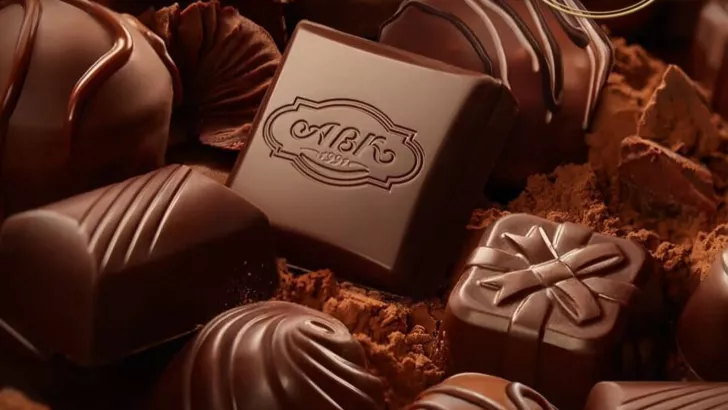
IDS Group
One of the leaders of the Ukrainian confectionery market. They are among the three largest confectionery companies in Ukraine in terms of production and in the top 100 companies in the world. Products are presented in 56 countries. AVK’s production facilities are located in the city of Dnipro. Products are manufactured on state-of-the-art high-tech equipment. The company’s production is certified by the international quality management system ISO 9000, ISO 22000. In 2017, high quality products were confirmed by the international standard IFS, which opened the possibility of selling sweets under the brand “AVK” in the retail space of the European Union.
Field of company activity:
Production, Distribution.
Trademarks:
“Royal Charm”, “Truffle”, “Truffle”, “Royal Masterpiece”, “Chocolate night”, “KRESKO”,”Bam-Buk”, “Major”, “Juviland”, “Chocolate AVK”, “Gulliver”, “Who told Mu?” and others
Tasks
Distribution automation;
Products that are implemented.
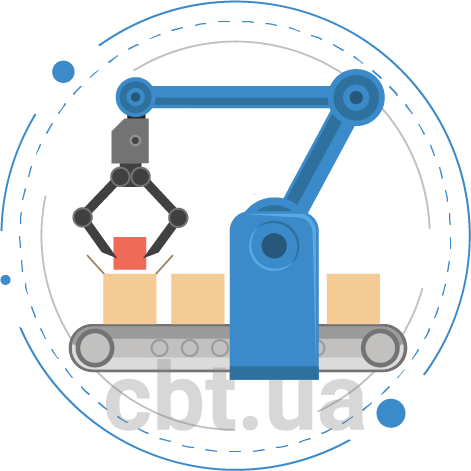
- FMCG
- Manufacturing
- Wholesale trade and distribution
- Transport, logistics, warehouse
- Pharmaceutics
- CBT products
- Inventory and supply management
- Planning
- Production Management (MES, APS)
-
Product added
to favorites -
Product added for
comparison
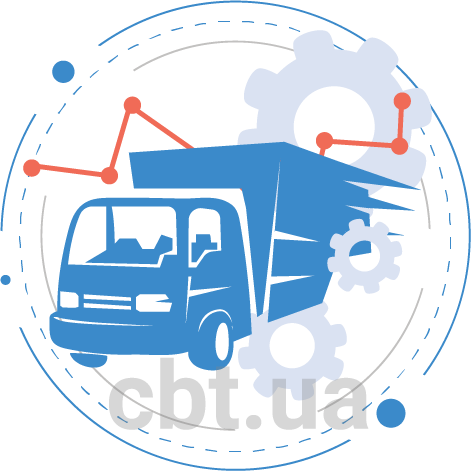
- FMCG
- Manufacturing
- Wholesale trade and distribution
- Transport, logistics, warehouse
- Pharmaceutics
- CBT products
- Inventory and supply management
- Planning
- Production Management (MES, APS)
-
Product added
to favorites -
Product added for
comparison
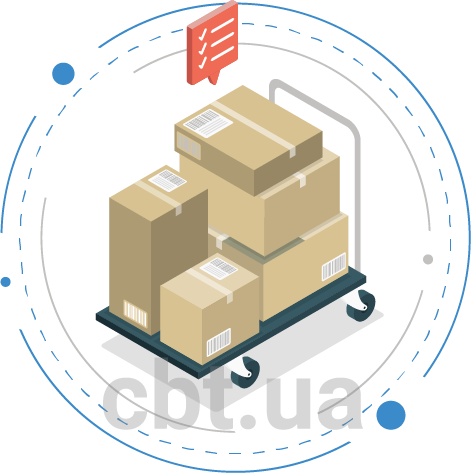
- FMCG
- Manufacturing
- Wholesale trade and distribution
- Transport, logistics, warehouse
- Pharmaceutics
- CBT products
- Inventory and supply management
- Planning
- Production Management (MES, APS)
-
Product added
to favorites -
Product added for
comparison
Areas of automation:
Product distribution planning
Production planning
Procurement planning of raw materials
Number of automated workplaces:
60 workplaces are automated
Have a
question?
Leave your contacts and receive
consultation from a specialist.
Download our full portfolio
Get the opportunity to learn more about our implemented products.
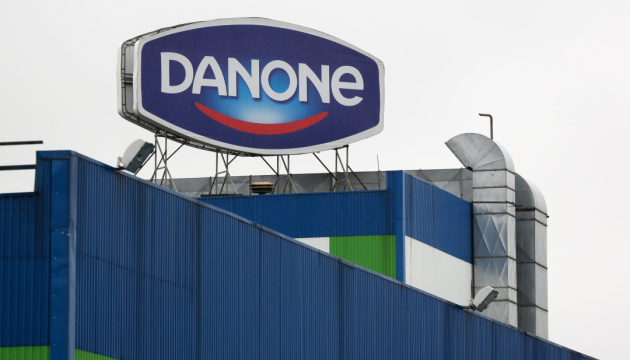

The SCM scheduling tool reduced the operational scheduling cycle to 1-2 hours per day, allowing several iterations of adjustments per day instead of 2 times a week earlier and only partial daily rescheduling; reduce the staff of planning managers from 8 people to 3 people; conduct in-depth analysis with fewer resources, and receive operational calculations instantly; reduce inventory levels by 30%!
At the same time to increase the level of customer support by 2-3%, which is currently 96-98%; We were able to increase the freshness of products for shipment to customers by 33% and reduce the level of write-offs of expired products in warehouses by 17%; strengthen control over the correctness of the tasks of the automated system through automatic calculations, visual inspection of inventory levels, analysis of changes in plans and incoming data. The implementation of the CBT SCM software solution has contributed to the growth of the business, and the results have exceeded our expectations.
Special algorithms have been developed for Danone Ukraine to take into account the specifics of production, storage and distribution of perishable, as well as shelf life management. Under these conditions, the response time to changes in needs or production plans may not be calculated in days or weeks to manage replenishment.
The SCM scheduling tool reduced the operational scheduling cycle to 1-2 hours per day, allowing several iterations of adjustments per day instead of 2 times a week earlier and only partial daily rescheduling; reduce the staff of planning managers from 8 people to 3 people; conduct in-depth analysis with fewer resources, and receive operational calculations instantly; reduce inventory levels by 30%!
At the same time to increase the level of customer support by 2-3%, which is currently 96-98%; We were able to increase the freshness of products for shipment to customers by 33% and reduce the level of write-offs of expired products in warehouses by 17%; strengthen control over the correctness of the tasks of the automated system through automatic calculations, visual inspection of inventory levels, analysis of changes in plans and incoming data. The implementation of the CBT SCM software solution has contributed to the growth of the business, and the results have exceeded our expectations.