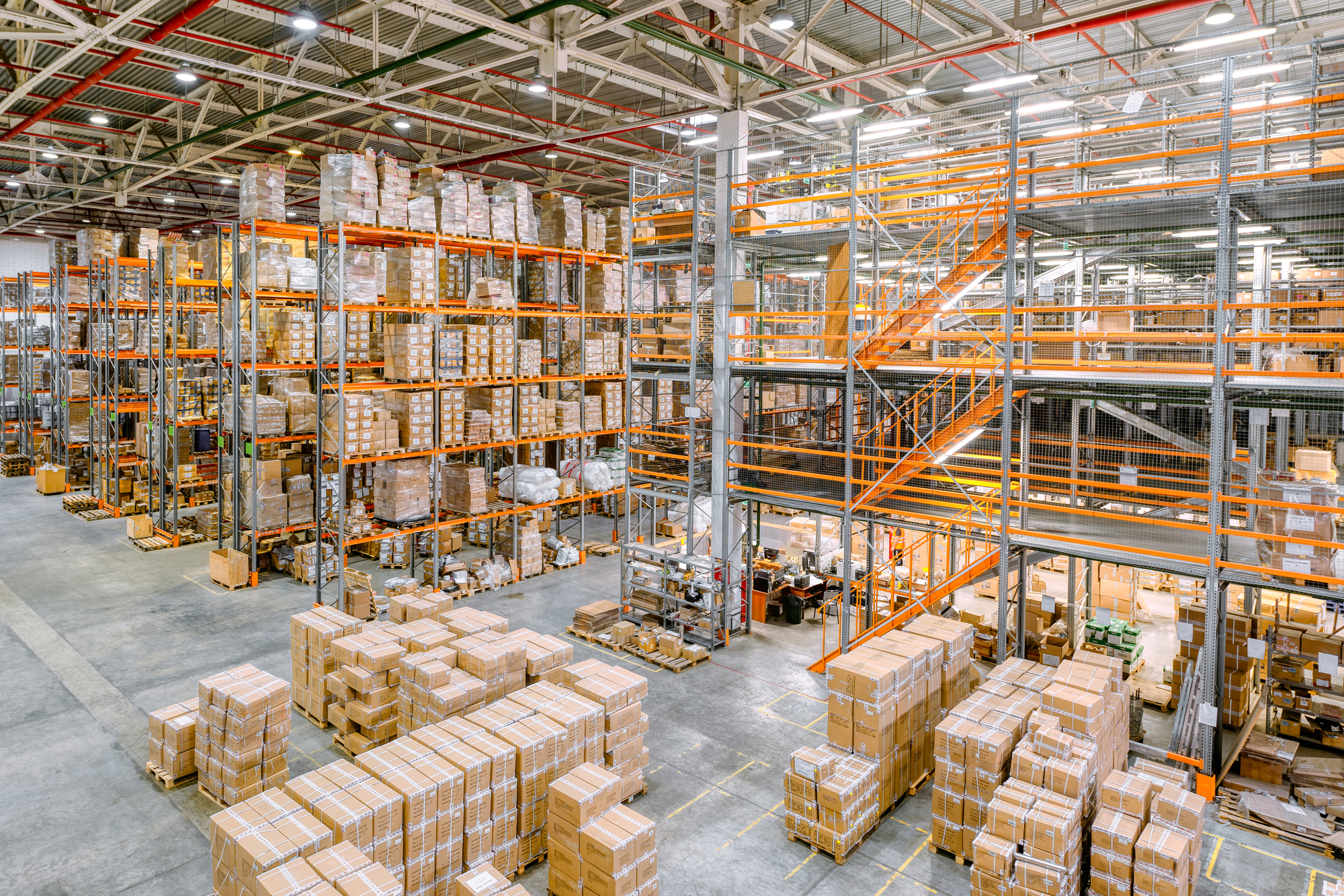
About product.
Case.
Reducing warehouse operations with a WMS-driven pipeline.
Implementation of a modern WMS system in the pharmaceutical company Delta-Medical
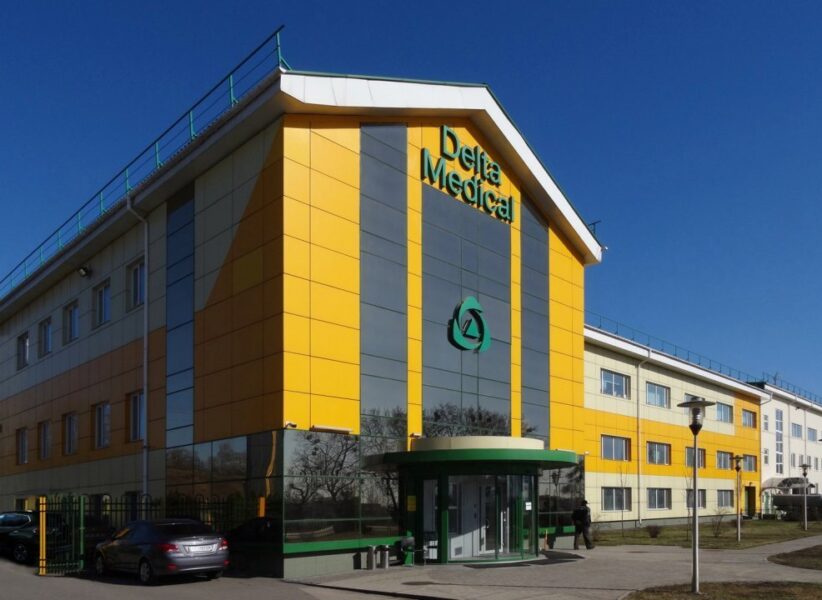

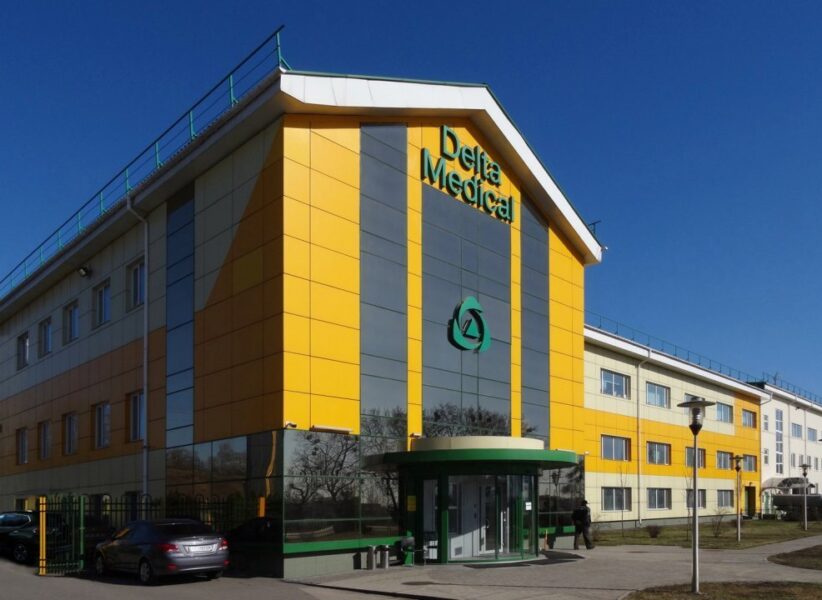

For whom.
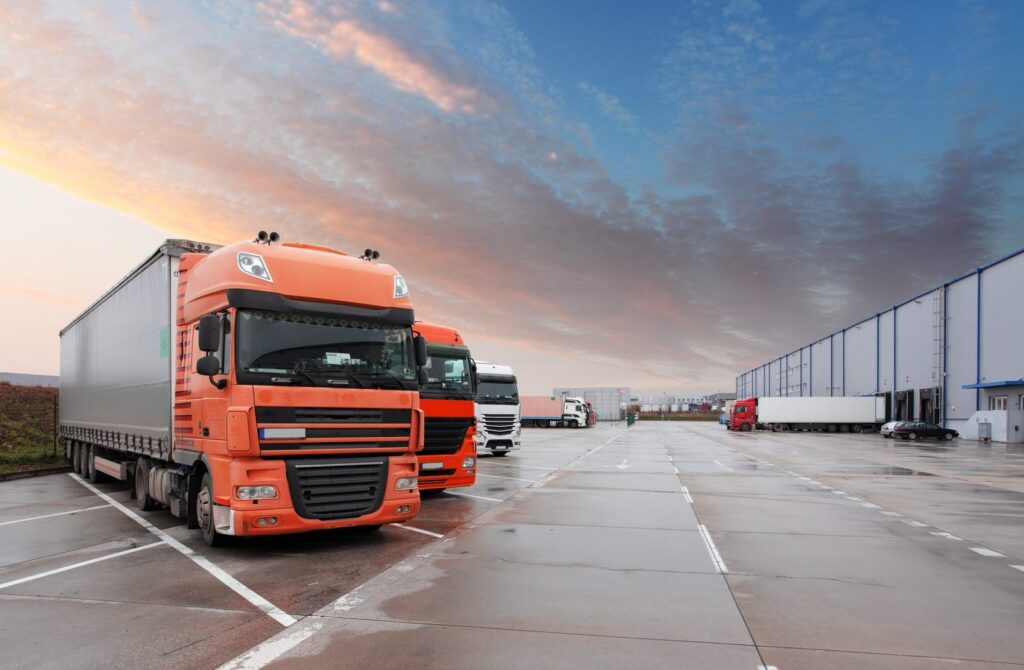
Managed by WMS Logistics. Warehouse management can operate warehouses of the following types:
Large wholesale or production warehouses with a small range. Arrival and shipment of goods is carried out in whole pallets
Small wholesale or retail warehouses of trading companies with a medium or large range. The goods come and go in any storage units (with possible packaging)
Warehouses of transport companies, which work with unique impersonal cargo
Warehouses for responsible storage. The composition of responsible storage can be any of the above warehouses
Capabilities of WMS Logistics. Warehouse management.
- Optimization of the use of warehouse space in the placement and storage of goods;
- reduction of storage costs;
- reduction of time and number of errors on processing of warehouse operations;
- Improving the accuracy and efficiency of goods accounting;
- Exclusion of losses associated with the critical timing of sales of goods;
- Reducing the cost of wages of warehouse workers.
«DistributionMaster-2021»
On October 29, 2021, the Center of Business-Technologies team speech at the DistributionMaster-2021 conference.
The topic of the report is “Improving the efficiency of warehousing processes using a collection pipeline and a modern WMS system. A practical case.”
Order a free presentation.
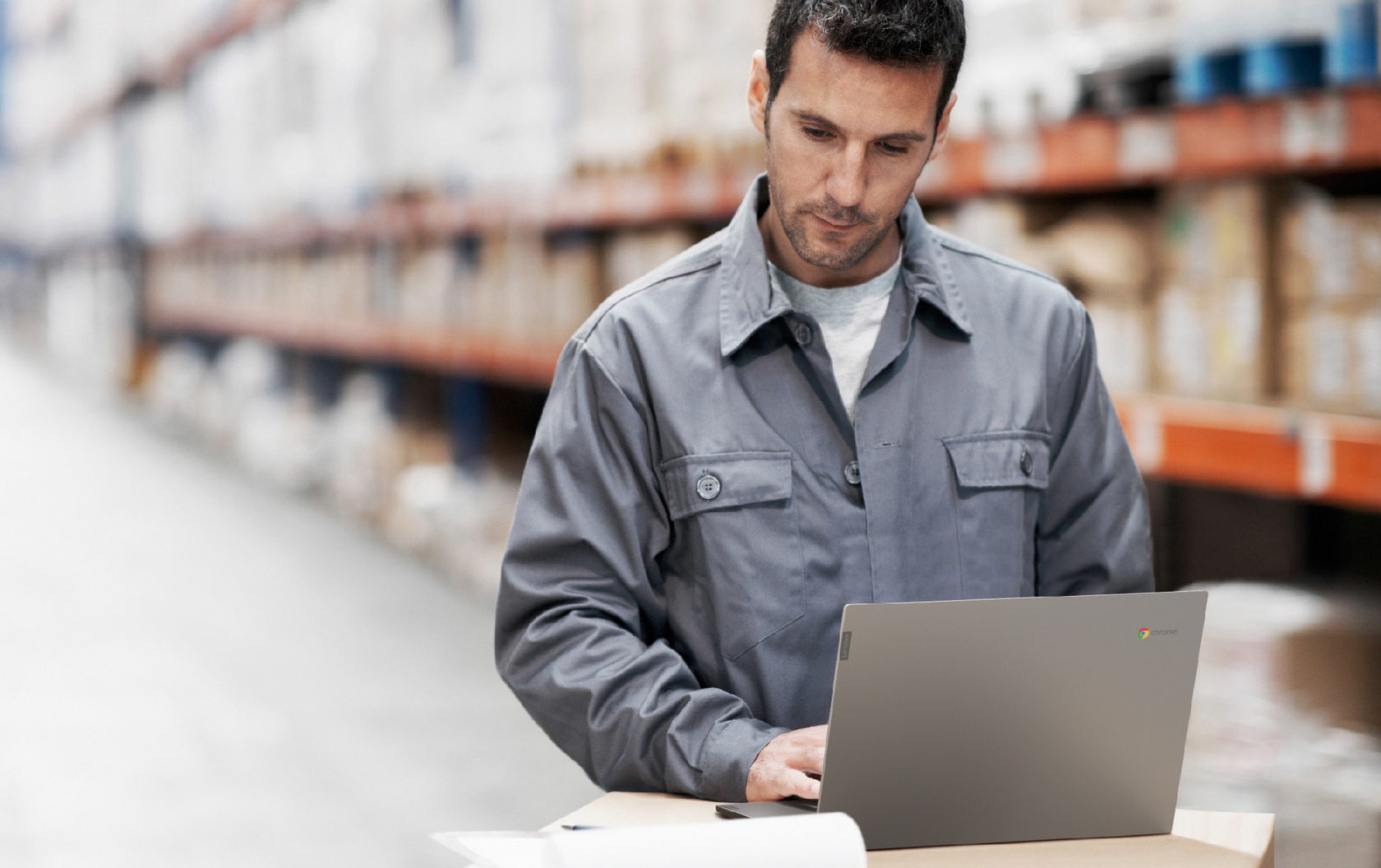
- obtaining up-to-date information on the balance of goods in the warehouse in the "online" mode;
- management and optimization of acceptance, placement, movement, selection, shipment and other warehousing operations;
- optimization of commodity flows in the warehouse;
- control over the work of warehouse staff.
Real-time warehousing process management is achieved through wireless technology and the introduction of an appropriate warehousing technology chain. Therefore WMS Logistics. Warehouse management is mainly aimed at the use of these technologies. The main functions for the creation and processing of warehouse tasks are performed by users with radio terminals for data collection: storekeepers, collectors, middle tiers. The function of the warehouse manager includes control over the implementation of tasks and solutions to non-standard situations.
The system can account for one physical composition. If it is necessary to operate the system on several physical or logical warehouses, it is necessary to create several information bases with the possible exchange of duplicate information.
The warehouse, as a rule, is divided into physical zones in which processing of the goods is subject to certain rules depending on a design of racks, the used equipment, planning of rooms, etc.
Warehouse zones.
-
Unloading area
The area is designed to accommodate goods arriving immediately after unloading from vehicles, such as a warehouse ramp. -
Quarantine zone (quality control)
The zone is intended for goods undergoing quality control, as well as for goods returned by buyers before deciding on their further movement. -
Selection Area
Product Selection Area. This is usually the lower tier of the cells or mezzanine. -
Condition zone
The zone is intended for goods with loss of appearance, with violation of the integrity of packaging, defective, expired, etc. -
Shipment Area
The area is intended for storage of goods to be shipped and cargo units until they are loaded into vehicles.
-
Reception area
The area is designed to list goods unloaded from vehicles and participate in the entry control procedure. -
Basic storage area
An area designed to store goods mainly in whole pallets. -
Transit Zone
Intermediate storage area. The transit zone can be allocated for temporary storage of goods when moving between zones. -
Assembly Area
The area is designed to assemble kits. -
Loading area
The area is designed to accommodate goods to be shipped and cargo units before they are loaded directly into vehicles.
Accounting for goods in the address space of the warehouse in terms of packaging (including non-fixed weight), expiration dates, batches, serial numbers, excise stamps, quality; accounting of containers and control of dimensions of goods; ABC / XYZ analysis; work with transit cargoes; excise accounting; work with cell blocks; accounting kits.
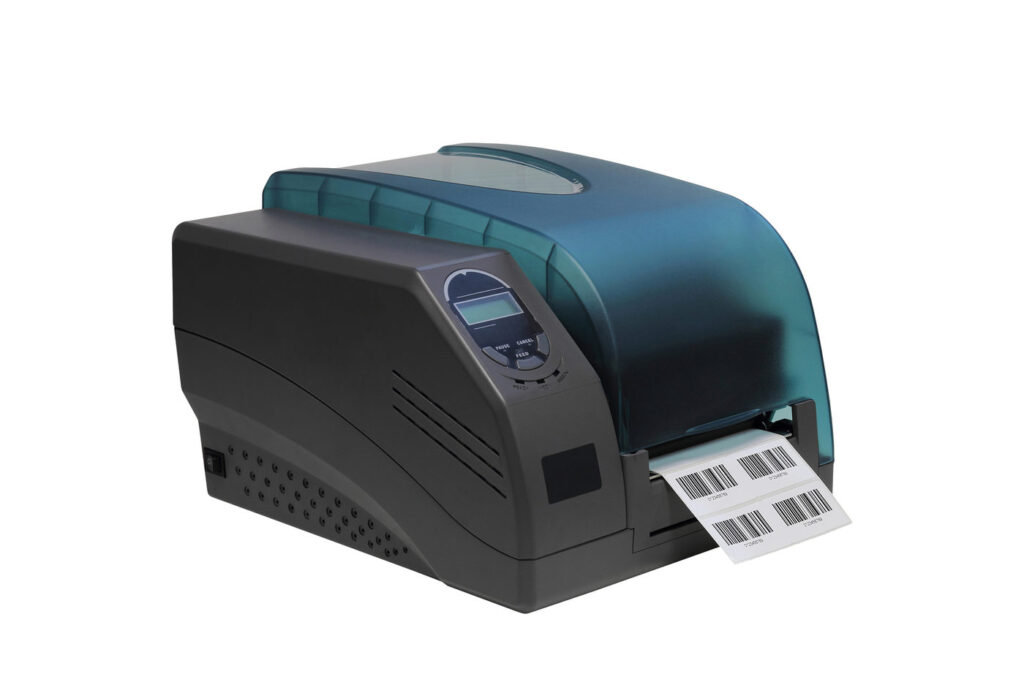
Accounting for goods in terms of digital labeling codes and traceability of goods in stock.
- obtaining ITC codes from the main accounting system. The ability to receive ITC codes outside the plan is regulated in the Adoption Strategy;
- the possibility of accounting for different nomenclature in terms of ITC codes - configurable at the level of the Nomenclature Accounting Model;
- movement of ITC codes within the framework of standard operations;
- conducting an inventory in terms of ITC codes;
- generating a report Balances in terms of the number of ITC codes with the ability to decipher the codes of consumer and transport / logistics packaging;
- possibility of generation and accounting of digital marking codes from own, accepted at the enterprise, system of marking of goods;
- the possibility of keeping records on one nomenclature both in terms of ITC codes and without - is configured at the level of the Lot of goods;
- the ability to track all intra-warehouse movements and balances of goods in terms of ITC codes;
- transfer of ITC codes to the main training system when performing operations on loading goods;
- formation of the report of the Movement of marked goods - displays data on all movements according to the given ITC code.
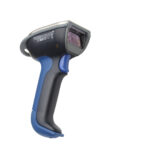
Acceptance. Acceptance in the trust mode and under the order (cross-docking), preliminary recalculation on places.
Placing. In the WMS Logistics system. Warehouse management can implement various product placement strategies: automatic, buffer placement, placement closer to the selection area; replenishment of the selection area during placement.
Moving. The process of internal movement of whole containers, goods between containers and cells in the system is made out with the help of movement tasks. Separate tasks are provided for the movement of entire containers and the composition of containers.
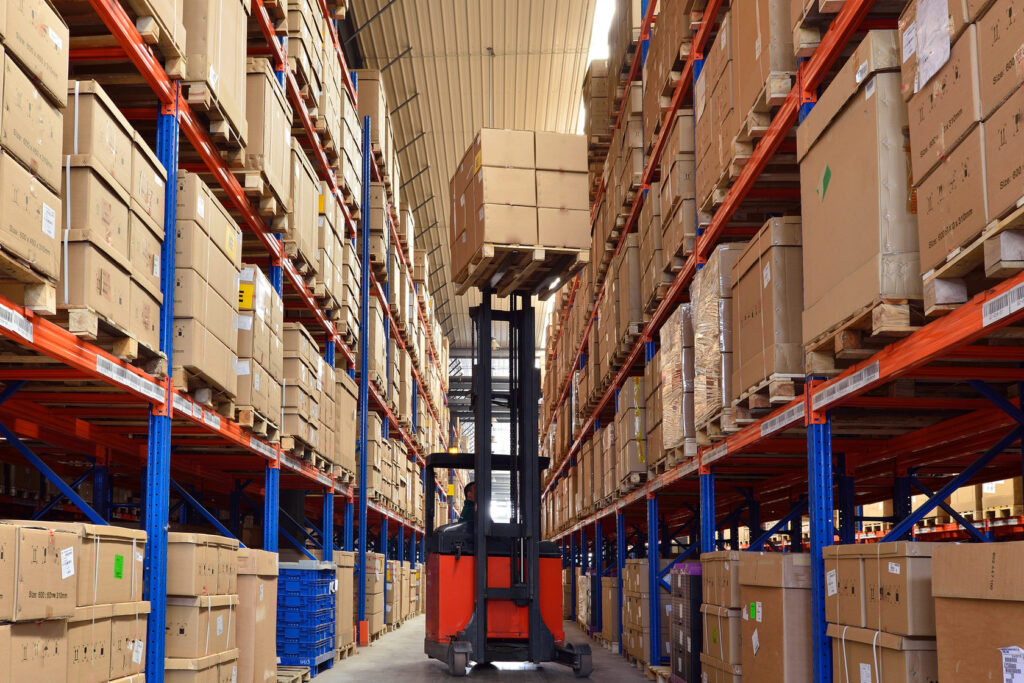
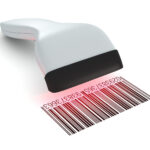
Bar coding of goods, cells, containers, personnel; generation, storage and printing of barcodes (barcode generation “GS1 DataBar Expanded Stacked” is supported); support for working with non-unique barcodes.
Selection and shipment of goods. Different selection strategies are implemented in the system: cluster, group; consolidation of selections in a wave according to temporary windows of shipment, in groups on similar goods, in flights on delivery routes.
Quality control of the accepted goods.
Quality control of selected and packaged goods;
control when loading into the car.
The system provides several types of tasks for recalculation:
- cell inventory. When conducting an cell inventory, all containers and goods located in the cell are subject to recalculation. At inventory of a cell recalculation both on quantity of containers in a cell, and on commodity structure of the container can be carried out;
- container inventory. When conducting an inventory of containers, the composition of a particular container for which the task is created is recalculated;
- inventory of goods. When conducting an inventory of goods, a recalculation of a specific product in all containers and cells in which the product is located;
- acceptance control. The task of acceptance control is intended for the transfer of newly accepted goods to the warehouse;
- shipment control. The task of shipment control is designed to recalculate the goods shipped to the customer's order from the warehouse;
- quality control. The task of quality control is designed to recalculate and check the condition of goods in the warehouse. Quality control can be carried out at any stage of processing of the goods: in the area of acceptance of the goods received, in the process of storage or shipment.
Inventory of any area of the warehouse, empty cells, product / product group.
Conducting an inventory using the WMS Logistics system. Warehouse management does not require a complete shutdown of the warehouse, and can be carried out on a limited area of cells (driveway, rack, tier) or a specific product group. The cell is not locked at the time of recalculation, which allows you to not stop working on the cell, which is inventoried for other warehousing operations.
Do you want to get a -5% discount on implementation?
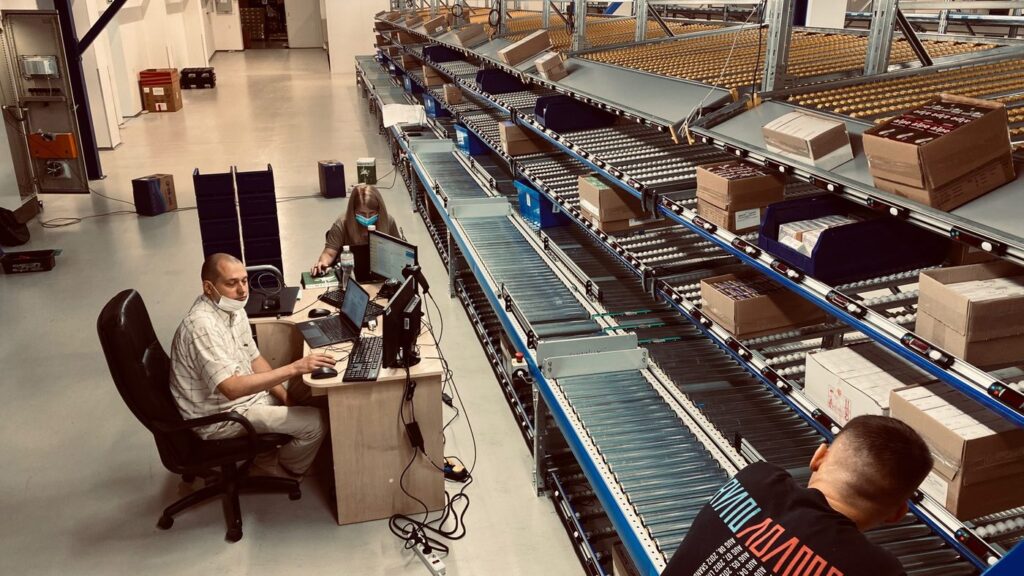
Optimization of the use of warehouse space – compression of the warehouse. To save space in the racks in the warehouse is usually a procedure for sealing the goods. Compression (or compaction) – moving goods from several cells to one in order to more efficient use of storage space. The compression strategy includes a list of compression algorithms and conditions for their execution.
Resource management.
- composition task management: classification and prioritization;
- assignment of access rights depending on the qualifications of staff and access zones;
- analysis of efficiency and productivity of personnel (KPI);
- fixing errors when performing warehouse tasks;
- control of tasks: fixation of the executor, duration, downtime;
- calculation of the required number of staff per shift;
- automatic distribution and issuance of tasks;
- calculation of warehouse staff production by volume, weight, number of operations;
- warehouse equipment management.
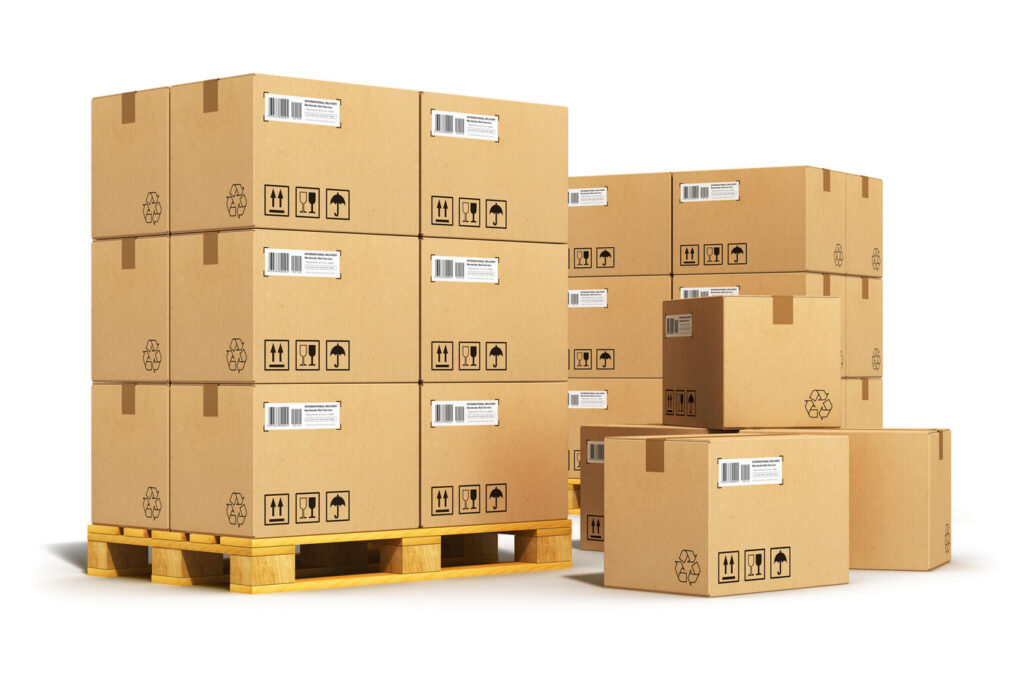
Calculation of responsible storage services:
- accounting for goods in terms of owners;
- setting tariffs for warehousing operations for each owner;
- calculation of the cost of services for each operation.
Analysis of the warehouse
effectiveness.
Due to the processing of warehousing operations, the functionality of the WMS Logistics system. Warehouse management allows you to perform:
- monitoring the status of orders and tasks to be executed;
- analysis of filling the warehouse in terms of storage zones and cells;
- analysis of the current state of the warehouse in terms of address storage;
- plan-factual analysis of the goods expected before entry and upon acceptance into the warehouse;
- plan-factual analysis of ordered and shipped goods from the warehouse;
- analysis of warehousing staffing.
Monitoring of orders and tasks is carried out with the help of workstations of dispatchers of reception, shipment and tasks. All analytical functions are implemented using reports that are developed using the data layout system and can be customized by users of the subsystem functionality. The reports are grouped according to the purpose in the respective configuration subsystems.
Successful cases.
The result of automation of warehousing processes at Delta Medical:
Delta Medical is one of the TOP-10 pharmaceutical companies in Ukraine, supplying products in Ukraine and Eastern Europe and Asia to more than 37 world-renowned manufacturers, including UPSA SAS, SCHONEN, AMGEN, BioGaia, GILEAD, URGO NUTRICIA, VITABIOTICS.
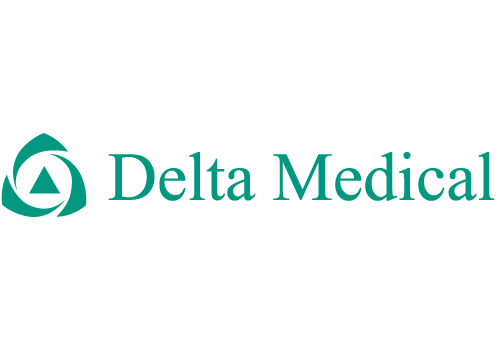
Based on WMS software, all Delta Medical warehousing processes are automated: acceptance and placement of goods, selection and control of wholesale and retail orders, shipment management, inventory management, monitoring and analysis of employees, etc.
The WMS system on the BAF platform manages the assembly line, the PickToLight assembly acceleration system (PTL) and other warehousing equipment, providing the highest level of productivity and control over warehousing operations and processes. The tasks created by the system are sent for execution to the data collection terminals (TSD) of warehouse employees, in its system controls their receipt and execution.
Together with our partners, we have developed an integrated order management system based on conveyors, gravity racks, weight control and a pick-to-light system, which provides high rates of speed and accuracy of customer orders. The introduction of automation has increased the productivity of selection by about 2 times, while significantly reducing the error rate. For example, more than 90% of the selection containers on the conveyor successfully pass weight control and are sent for packaging without detailed recalculation.
Our team continues to develop and improve the capabilities of the system.
The Center of Business Technologies Group of Companies is a team of qualified specialists with extensive practical experience in implementing complex systems for business automation.
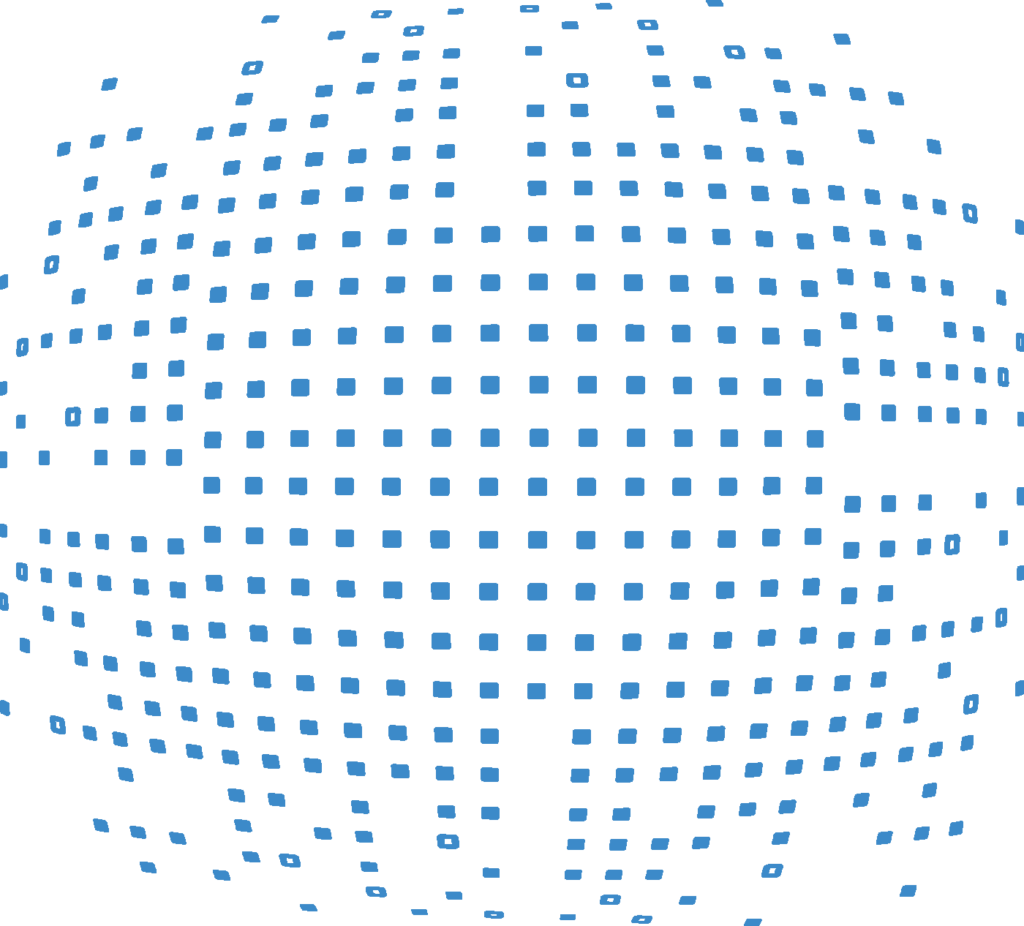
Team.
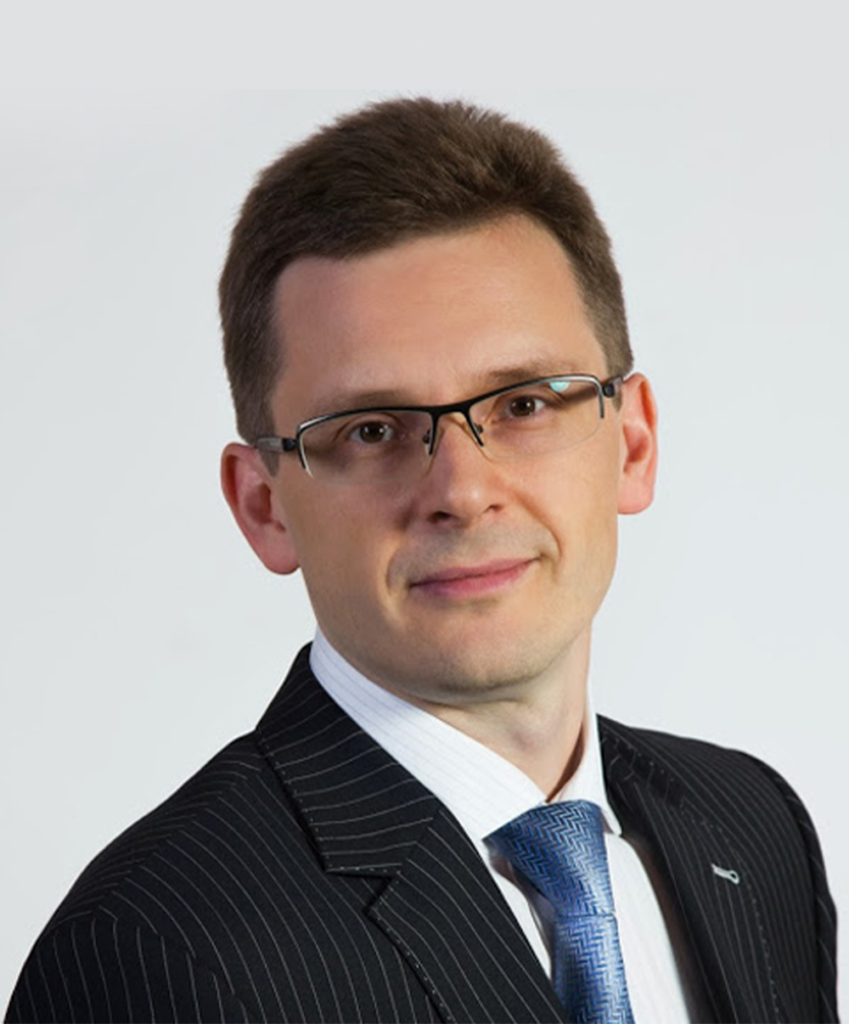
Andrii Pecherskykh
Director,
expert in warehousing logistics
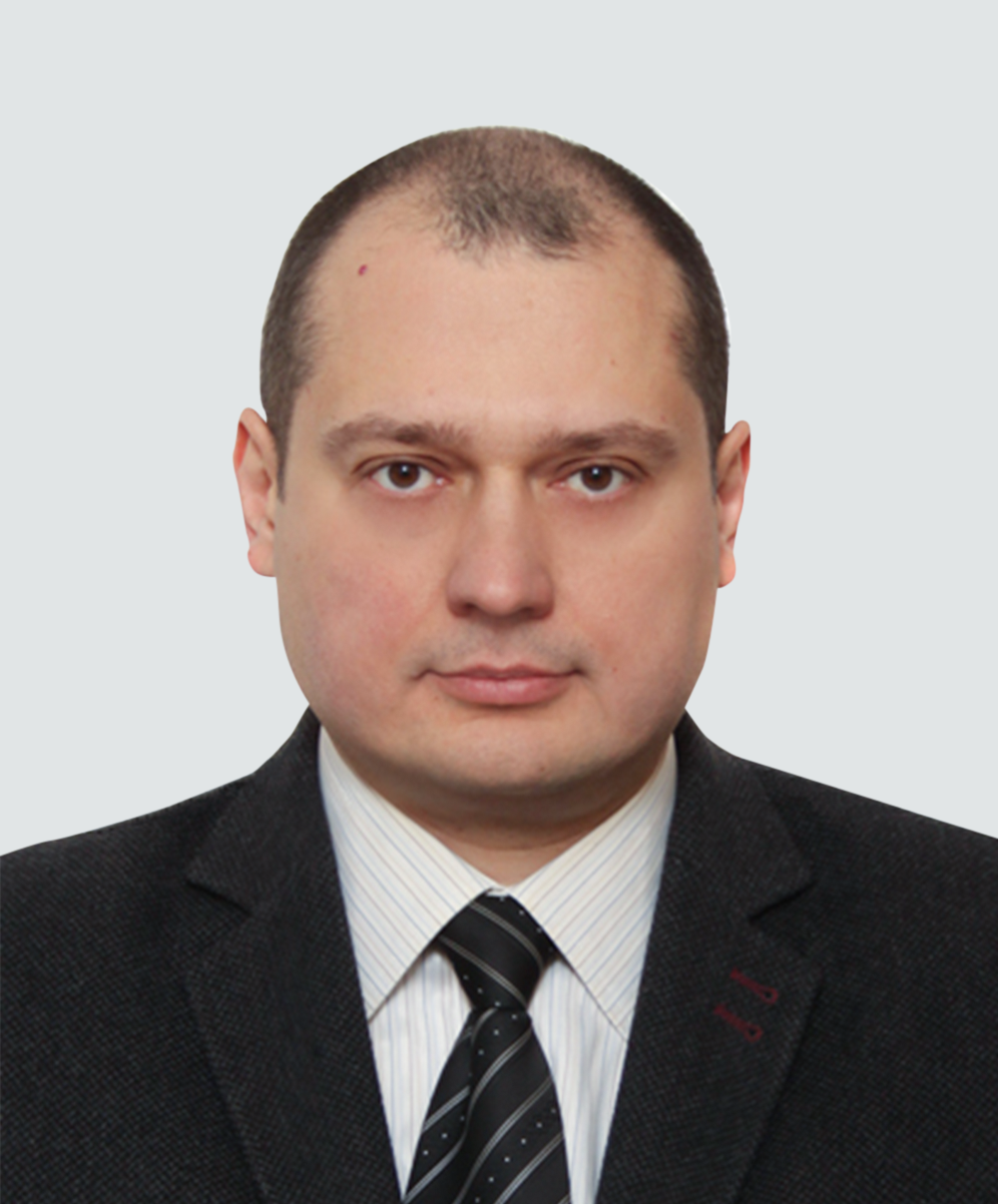
Alexey Shushura
Doctor of Technical Sciences,
expert in warehousing logistics
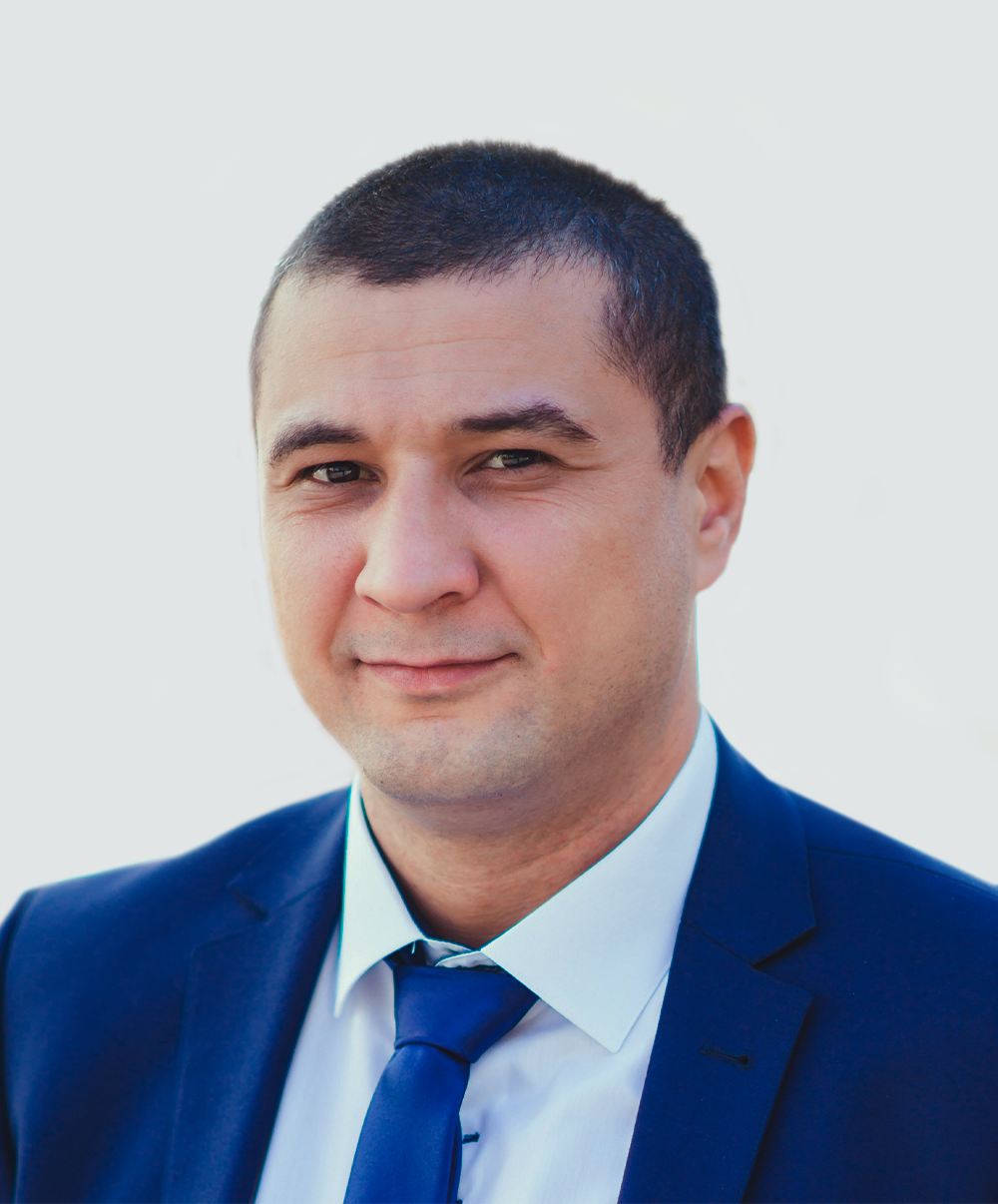
Sergey Lysenko
Head of Sales
About us in numbers.
jobs